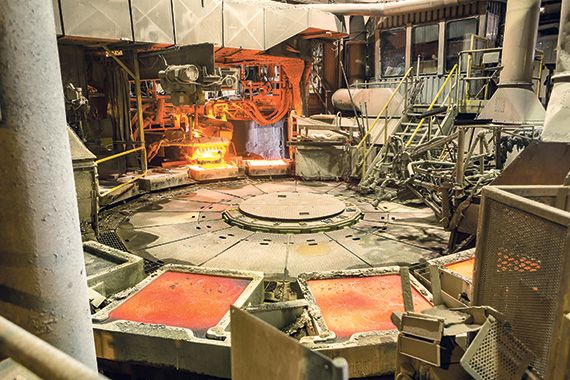
À la Fonderie Horne, les concentrés de cuivre sont dosés selon une recette et acheminés dans un réacteur, où ils sont chauffés à une température de 1 200 °C.
La Fonderie Horne surplombe depuis toujours la ville de Rouyn-Noranda, baignée par le lac Osisko. Sur un immense site de plus de 2 km2, des camions et des wagons circulent sans cesse pour y décharger les quelque 700 000 tonnes de concentrés de cuivre provenant de mines, et d'autres matériaux contenant du cuivre et des métaux précieux, qu'elle reçoit chaque année. Sans oublier les 100 000 tonnes de matériel électronique en fin de vie qui y sont acheminées pour récupérer le cuivre et d'autres métaux précieux.
«Nous sommes aujourd'hui le plus grand producteur de cuivre et de métaux en Amérique du Nord», dit fièrement Claude Bélanger, directeur général de la Fonderie Horne depuis 2006.
Lorsque l'explorateur Edmund Horne a découvert un énorme gisement d'or et de cuivre dans les années 1920, il était loin de se douter que, 90 ans plus tard, la fonderie portant son nom serait devenue la seule fonderie de cuivre du Canada, alors qu'il y en a une cinquantaine dans le monde.
«La crise économique de 2008 a fait mal. La demande pour le cuivre a chuté, et plusieurs fonderies ont dû fermer leurs portes», explique M. Bélanger, en précisant que la Chine a par ailleurs multiplié les usines qui traitent le minerai à moindre coût. «La compétition est forte et il y a aussi moins de mines en exploitation au Canada, ce qui réduit nos sources d'approvisionnement», souligne-t-il, néanmoins persuadé de pouvoir célébrer le 100e anniversaire de la fonderie en 2027. La Fonderie Horne, qui emploie 550 personnes, appartient au géant des ressources naturelles Glencore depuis l'acquisition de son ancien propriétaire Xstrata en 2012.
L’oeuvre de Sébastien Ouellette et Lancelot St- Amour installée à Rouyn-Noranda est faite de cuivre et d’acier et a été réalisée en collaboration avec la Fonderie Horne.
En 1976, après 50 ans d'exploitation, la fermeture de la mine Horne, située sous la fonderie, avait aussi donné un dur coup. La fonderie réussit toutefois à demeurer active en traitant le minerai issu d'autres mines. Elle diversifie aussi ses activités avec la mise en service d'une unité de recyclage des matériaux électroniques.
«On récupère notamment le cuivre, l'or, l'argent, le platine et le palladium provenant de matériaux électroniques en fin de vie qui, autrement, iraient à l'enfouissement ou dans des pays sous-développés», indique M. Bélanger. En 2015, la fonderie a récupéré 26 500 tonnes de cuivre et 1,6 million d'onces de métaux précieux à partir de 106 000 tonnes de matières recyclées.
Les matériaux électroniques recyclables viennent principalement des États-Unis (54 %) et de l'Europe (34 %), alors que le Canada en fournit seulement 8 %, dont 4 % du Québec. Par ailleurs, les concentrés de cuivre arrivent principalement des mines canadiennes (80 %), ou encore des États-Unis (13 %) et d'outre-mer (7 %). Environ 85 % des matières premières utilisées par la fonderie sont des concentrés de cuivre. «Il y a un fort potentiel de croissance pour la récupération des matériaux électroniques», fait valoir M. Bélanger.
Toutes ces matières sont dosées selon une recette et acheminées dans un réacteur, où elles sont chauffées à une température de 1 200 °C. Après avoir atteint une teneur en cuivre de 70 %, elles sont transférées dans des convertisseurs et des concentrateurs pour obtenir du cuivre pur à 99,1 %. Le cuivre ainsi obtenu est moulé en anodes de 340 kg qui sont transportées vers l'affinerie CCR, à Montréal-Est, une autre propriété de Glencore, pour une dernière étape de transformation. Le cuivre sera purifié à 99,99 %, puis vendu sur le marché.
«Ce métal est encore très présent dans notre quotidien. On en trouve évidemment dans les tuyaux de maisons ou de certains toits de bâtiments, mais il y a de plus en plus de nouvelles applications», souligne M. Bélanger.
L'utilisation du cuivre est ainsi de plus en plus répandue dans les diverses technologies, comme les piles solaires, les panneaux chauffe-eau ou encore les véhicules électriques. «Le cuivre, avec ses propriétés antibactériennes, pourrait aussi être efficace dans les hôpitaux», ajoute le directeur général.
Pour assurer sa pérennité, la Fonderie Horne investit d'importantes sommes d'argent. Depuis 2011, ses investissements totalisent 300 millions de dollars dont le tiers est consacré à des initiatives environnementales. «L'entreprise a fait des actions concrètes pour réduire ses émissions atmosphériques», indique Stéphanie Lemieux, coordonnatrice des communications et des relations avec la communauté à la Fonderie Horne.
En 1989, en réponse à des pressions de la population visant à l'inciter à ne plus rejeter de soufre directement dans l'air, la Fonderie Horne s'est dotée d'une usine d'acide sulfurique. En 2016, elle a d'ailleurs atteint un sommet de 96 % de captation du soufre. Depuis 2004, elle a réduit de 71 % ses émissions de SO2. La Fonderie Horne produit même plus de 600 000 tonnes d'acide sulfurique qui est distribué en Amérique du Nord et utilisé principalement pour des fertilisants, mais aussi dans les industries pharmaceutique et de l'alimentation.
À la fin de juin, pour promouvoir le recyclage parmi ses employés et la population, la fonderie a mis en place un point de dépôt de matériel électronique et électrique en fin de vie. «On reçoit des ordinateurs, des cellulaires, et c'est toujours rempli. Ça nous permet de leur donner une deuxième vie», se réjouit Stéphanie Lemieux. Celle-ci s'affaire aussi à organiser les festivités du 90e anniversaire de la Fonderie Horne, qui aura alors produit plus de 12 millions de tonnes de cuivre, 40 millions d'onces d'or et 847 millions d'onces d'argent !
550
C'est le nombre de personnes employées par la Fonderie Horne, qui appartient au géant des ressources naturelles Glencore depuis l'acquisition de son ancien propriétaire Xstrata en 2012.