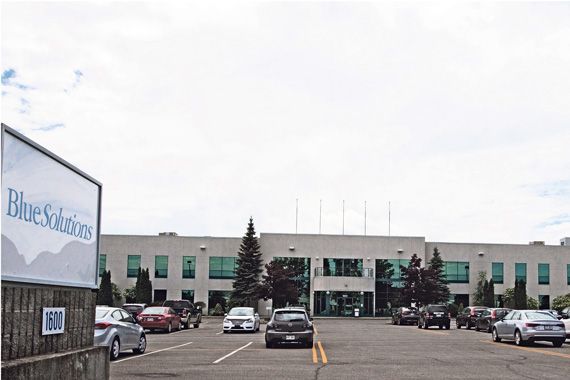
Les technologies d'automatisation pourraient générer des gains de productivité de plus de 10 %, estiment les 619 professionnels des ressources humaines sondés par Konica Minolta Business Solutions. Quels systèmes automatiser en premier, comment limiter les coûts et que faire pour réussir son virage ?
Pour éviter de subir des dépassements de coûts, une entreprise doit d'abord savoir ce qu'elle désire automatiser et améliorer dans sa production, puis choisir en fonction de ce qui amènera une plus-value. Dans le domaine manufacturier, les fonctions qui sont automatisées le plus souvent sont les tâches répétitives. Dans les centres de distribution, ce sont toutes les tâches reliées à l'emballage et à la manutention. En alimentation, il s'agit de tout ce qui touche à l'augmentation de la qualité ou à la diminution des pertes.
«Si on a un problème de cadence, on n'automatisera pas les mêmes équipements que si on a un problème de qualité», explique Mathieu Charlebois, consultant chez Automat Solutions, une entreprise basée à Les Cèdres et spécialisée en automatisation industrielle. Il raconte qu'un client lui avait un jour demandé d'automatiser ses équipements pour pouvoir mesurer, manipuler et marquer automatiquement l'ensemble des pièces qu'il fabriquait. Cependant, les pièces mesuraient de quelques millimètres à plusieurs mètres et le client voulait une précision de l'ordre du micron, soit la moitié de l'épaisseur d'un cheveu. «Il croyait que ça lui coûterait 100 000 $, dit Mathieu Charlebois. C'est un projet qui lui aurait en réalité coûté plus d'un million.»
Que faire dans un cas comme celui-là ? M. Charlebois estime qu'il faut automatiser seulement une portion de la production, soit les systèmes les plus critiques ou ceux qui représentent le goulot de la production. Il peut également s'agir des opérations les plus longues, les plus dangereuses, ou de celles pour lesquelles il est le plus difficile de trouver des employés.
Les projets de rénovation ou de modernisation, aussi appelés «rétrofit», sont généralement ceux qui sont les plus susceptibles de générer des dépassements de coûts et d'autres mauvaises surprises. Les causes de telles situations sont parfois plutôt banales. Mathieu Charlebois remarque que le câblage des capteurs, notamment, crée souvent des imprévus coûteux. Il peut s'agit d'une usine de filtration d'eau, par exemple, qui désire automatiser ses équipements, mais qui oublie, au moment de la planification, de mentionner une machine qui se trouve à quatre kilomètres de là, dans le poste de pompage.
Améliorer la traçabilité
Blue Solutions fabrique des batteries à grande capacité pour les véhicules et le stockage d'énergie solaire ou éolienne. Elle fabrique notamment des batteries pour les voitures de marque Bluecar qu'utilise Autolib', le service parisien d'autopartage de voitures électriques en libre-service. Depuis 2007, elle a procédé à l'automatisation de son usine de Boucherville, explique Jean-Luc Monfort, le directeur général de Blue Solutions, conférencier à l'événement Usine 4.0 organisé par le Groupe Les Affaires le 19 septembre.
Son entreprise désirait entre autres augmenter la traçabilité de ses batteries. Elle a donc mis en place un historique de production, soit un système qui récolte automatiquement des téraoctets de données au sujet des matières premières et des paramètres de production des batteries : température à la fabrication, composantes utilisées, source du lithium métal, etc.
«En pratique, tout cela devient très utile pour pouvoir mieux analyser la performance des batteries en fonction de leurs caractéristiques de production et ainsi faire progresser la R-D», dit Jean-Luc Monfort.
Un exemple ? Disons que Blue Solutions examine une batterie défaillante. Elle sait qu'il s'agit de la batterie numéro 1324, livrée le 12 octobre 2011, et qu'elle a fait 200 000 kilomètres sur une voiture à Paris. Sur les 120 cellules, elle remarque que c'est la cellule numéro 112 qui a failli en premier. L'entreprise peut donc analyser les paramètres de production de celle-ci pour tenter de déterminer la cause de la défaillance et améliorer sa production.
Un océan d'informations
La capacité de production annuelle de l'usine de Blue Solutions s'élève aujourd'hui à 10 000 batteries. Elle devrait être de 32 500 batteries en 2019-2020. Pour réussir son automatisation, Blue Solutions a toutefois planifié l'ajout de fonctionnalités sur plusieurs années. «Il faut connaître ses priorités pour savoir quoi automatiser», dit Jean-Luc Monfort.
Plusieurs gestionnaires pensent qu'il vaut mieux tout automatiser et récolter le plus de données possible, et que les résultats ou les améliorations potentielles sauteront aux yeux, explique Mathieu Charlebois.
«Cependant, on se retrouve alors souvent avec une quantité phénoménale de données, dit-il. C'est important de savoir quoi mesurer et automatiser, sinon on se noie dans les données. Plus on planifie, plus on diminue les coûts, plus on atteint nos objectifs rapidement.»